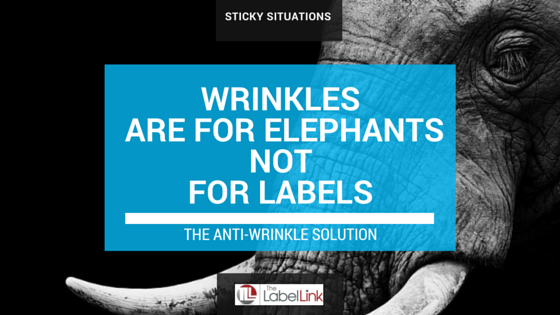
Peel and stick. Seems simple enough. Yet when the fit is off, you’re using the wrong adhesive, or the temperature changes, you could be faced with an unexpected problem – wrinkles.
Wrinkles are never a welcome sight. On clothes, skin, and labels wrinkles give the look being old, worn and unkempt. Is that how you want your brand to look to your customers? Probably not.
Here are a few ways to keep your labels from wrinkling.
Find the Right Fit
Every bottle, can, and container are shaped differently. As your label hugs the side of your product’s packaging, it has to fit in just the right way. If not, it’ll wrinkle.
Before you place your order, make sure the dimensions are suitable for the container in which you are labeling. You must have a clearance from any of the curves or bottle shoulders. This clearance is generally about one-eighth of an inch, give or take from all sides.
In addition, you’ll want to ensure the surface is flat, or it has a large curve. Trying to squeeze your label snuggly over a tight corner will make it hard to uphold its visual appeal.
Application
The way your label is applied is equally as important. Just because a label fits properly doesn’t mean it’ll go on smoothly.
One of the best ways to avoid common application issues is to have a large enough wipe blade. This will help you keep everything smooth and even as you apply your label.
You should also steer clear from high tack adhesives that stick too quickly. This type of adhesive doesn’t allow you to properly place your label before adhering tightly, causing gaps and wrinkles. Instead, opt for an adhesive that allows you to reposition the label while you’re applying it to the product. This type of adhesive will build adhesion over time, usually within the first 12 – 24 hours after application.
Watch the Mercury
The type of material you’re applying your label to matters. Plastic bottles expand and contract with the temperature. Your label will appear to be applied smoothly, then a few hours later, it’ll start to wrinkle because the temperature changed.
To avoid this natural size change, your must apply your label in a way that can move with the bottle as the mercury rises and falls. The trick is to use a repositionable label. This type of adhesive is softer and takes more time to bond, allowing the label to move naturally with the plastic containers and bottles.
Another consideration is to use a similar type of material so that it also moves and contracts with the container. For example, it would be better to apply a polypropylene label to a polypropylene bottle. A paper label on that same container may tend to wrinkle more as paper does not expand/contract when the mercury rises or falls.
The bottom line is this. You can’t afford to send products filled with wrinkled labels to market. With the right fit and the right adhesive, you can sleep better at night knowing your labels will always look good from the storeroom to the shelf and beyond.
Question: Have you’ve ever seen a product on the shelf with wrinkles, what was your impression? Please note your answer in the comments section.
Wrinkles happen to the best brands. It’s nothing to worry about, but it is something you can actively work to avoid.
We have the anti-wrinkle solution team. Shoot us a quick email with your particular application issue and we will be happy to reply to you with some troubleshooting ideas. And, if you like these tips and want more, direct to your inbox, don’t forget to check the box when you send us that email.
Hi I have a wrinkling problem with labels. PP labels are being stuck on to a PP bottle immediately after it has been hot filled at 80 degrees C. Labels are wrinkling after application. I’ve tried various other options like PE and PO and even paper which is a long shot with no success. The bottle is curved and hence the label is also curved and fairly large. Any ideas??
Hi Sally,
Thanks for your inquiry. Often times, the adhesive is also a factor. So I cannot say, as I need a bit more infomation. You mention that your hot fill is at 80 degrees C = 176 F, which is very close to the upper limits of most pressure sensitive adhesives. A PP film is thinner and may show wrinkles more easily. , I do agree with your reasoning to consider PE or PO materials as they are thicker and more conformable, but the adhesive used, is also critical. Other factors that we need to understand are the size of the label and how they’re applied to the container. Is it a wrap or front/back panel? How much dwell time is there before the wrinkles develop? There are so many variables that can cause this.
Certainly hot fill is a tricky one, but not a puzzle that cannot be overcome. The ultimate solution may require a custom material with hihgher minimums. So your label quantities (or your budget) would determine what materials are an option.
Custom applications often require custom solutions. There is not typically a one size fits all solution. But be encouraged. I’ve seen many issues like this resolved.
I’ll reach out to you directly for a more detailed conversation.
Thanks,
Rosalyn
Trying to solve a similar problem. But customer is using hdpe bottles. Filling citrus juice but labels are wrinkling also. Tried two different bottle manufacturers on the same style bottle. Can you please try to advise if it’s an adhesive problem / bottle resin or gram weight issue?
Hi
I think you must try PET or PVC which have more dimensional stability in presence of hot surface.
Thank you Mohammad
I appreciate your comment and I agree that dimensional stability may help. However, paper is often most dimensionally stable (it doesn’t expand and contract with heat) yet Sally mentioned that, it too, is wrinkling.
The key is to test each variable, one at a time, as there is no one-size-fits-all solution. My concern is that since the bottle is PP, it will expand and contract as it heats and cools. If the label cannot move along with the bottle at the same rate & the adhesive is overly aggressive, a wrinkle can be introduced. In this case, the combination of the label substrate/adhesive combination is important. So if bottle expansion is the root cause, then PET may not be a solution as it is rigid and tends not to conform. However, PVC could be a candidate as it too would conform.
Unfortunately, I didn’t have enough information on this application. The wrinkles could be caused by a wrong sized label or a misapplication & not the heat. However, I would need more details to know. PET is a good option for high heat applications when the container is rigid. The adhesive also has to withstand the high temperatures, too.
I appreciate your suggestion. Thanks for reaching out to offer assistance.
Hello, I am a blow molder of HDPE and PET bottles like aspirin and vitamin bottles. Also jars for the supplement health powders from 16oz jars to 32oz jars. I am having a big problem with all of these fillers using foil labels with a paper backing on the PET jars. They are wrinkling. I have identified that a lot of them have oversized the labels getting very close to the radius of the shoulder and base of the jar. they are almost all using in-line labelers with moving applicator pad and stationary back pad. We fight wrinkles constantly with the foil labels. Any minor out of round with the bottles also causes wrinkling. Any tips to help on labeler set up?
Hello Terry,
Thank you for reaching out. There could be many reasons for this to occur. I would be happy to discuss more specific details with you directly. It sounds like your client(s)/fillers are having the issues when applying them in their plants?
The label size is crucial and must not be oversized. Are the foil labels metallized film or laminated foil on a paper-backed facestock? I’m not referencing the liner here but if you look at the adhesive side, is it paper or foil? If they can go with a laminated foil/paper product, that may be a more forgiving option. Static electricity and very thin films can prove to create challenges if the surface is not just right. Out of round bottles will definitely create an issue.
I will email you directly to talk further about your specifics.
Hello, we have a complaint from our customer saying that our labels is crumpled when they pasting to their final product. We are using (sorry to mention the brand and type) 3M#3690E with clear lamination on top of the facestock. We have doing internally testing with high temp, rubbing with IPA, simulation as per warehouse and transportation condition, but there is no crumple as per customer claim. I have no idea why it happen since our internal testing showing the result is pass and no changes from initial and after testing.
FYI, the based material is 3M#3690E with clear lami but we have testing using others type material such as OPP lami, thermal film, PET 16 and 25 but all of them is pass without crumple.
Any idea why the label will crumple after pasting?
Hello,
We are pasting paper (PP chromo paper, pressure sensitive ) labels on HDPE moulded bottles having flat surface. We use auto applicator to paste the labels.
When we apply labels there is no issue. But after 2 -3 days, they develop wrinkles and flagging.
Please suggest remedy and reason for same.
Hello Sunil,
Thanks for reaching out!
I cannot say for sure as I’m unclear what your stock is. You say you use a paper label but then say it is (PP chromo paper/ps). Usually, PP stands for Polypropylene which is a RIGID film and not paper. Not quite sure what you mean by “chromo”, either. Is the material chrome metallized? If so, these are not paper but rather film. (Unless it is a laminated foil to paper???). Needless to say, there are multiple materials out there and they definitely have an impact.
Here are some of my thoughts that you may want to consider:
* Since you are applying labels to HDPE containers (usually squeezable), it could be that the container is either contracting (due to cold) or expanding (due to heat) while the label is not adjusting at the same rate. This is potentially a result of either, 1) the content is filled at a different temperature than the environment (hot fill or cold fill) or, 2) the storage is an extreme temperature (freezer or in a hot environment).
The reason wrinkles show up later is that it takes time for the HDPE to expand/contract to the environment. Also, if the adhesive is too aggressive, the label cannot move with the container.
It could also be that your label is too rigid of a stock for the HDPE and it doesn’t move as well.
Possible tests that you can check (not in any particular order):
1. Try labeling the EMPTY container in advance and filling 24 hours later to allow the labels to stabilize.
2. Consider using a more conformable & pliable film, vinyl-like, facestock – PE, MDO or Polyolefin facestocks.
3. Try applying a label with a softer adhesive.
4. Ensure that your label is not too large for the surface area (generally, you want at least 1/8″ clearance around the application area).
5. Ensure that your applicator is getting a clean lay down of the label and that it does not have air pockets that can show up later.
6. Oddly enough, if you are actually using a film product (and not a paper facestock), I have found that the paper facestocks sometimes perform with fewer wrinkles because it is porous and any air would not get entrapped like on a film product. So it is something to try.
Again, there are always specific areas to consider in something like this and they are best handled on a case-by-case basis, but I hope that this gets you going.
Best wishes,
Rosalyn
I work in a packing facility were we fill 55 gallon drums. We place customer product labels on the drums. We have many different customers and different labels. Due to the large variation it is not economically feasible to automate the process. Is there some equipment that can be used to assist the operators?
Tim
Dear Sir,
We have oil filled PET bottle stock and we are facing lable peeling and wrinkle problem due to oil leakage from some bottle, so we are going to change new label of that stock, but due to oily surface label are not adhesion properly and peel off again, so please guide us and give us the right solution for this stock, because we have huge stock of this and due to this our sale is stopped.
Thanks & Best regards,
Qasim Raza Shoukat
Labels will not stick to an oily surface. You will need to figure out a way to clean the surface before applying the labels and preventing the oil from spilling.